铝镁质钢包浇注料的抗渣性能受哪些原料的影响
- 发布人:中国镁质材料网
- 发布时间:2022-11-25
- 浏览量:530
70年代,钢包仅作为输送钢水的容器,因而使用廉价的酸性耐火材料,并逐渐过渡到高铝砖耐火材料等。现在,钢包已经成为重要的精炼设备,因而碱性砖成为钢包内衬重要的耐火材料,并且以不同的施工方法配合使用,例如渣线用MgO-C砖,在包底和包壁用铝镁质浇注料。渣线部位的使用条件特别苛刻,其内衬损毁也最为严重。在实际应用中,应特别注意钢渣对耐火材料的损毁。
钢渣对耐火材料的损毁主要分两个方面,一是侵蚀,二是渗透。当渣渗入到砖中,在砖内形成变质层,变质层与未变质层在使用过程中不断的冷热温度交换,膨胀系数的差异导致产生裂纹并出现结构剥落。因此钢包浇注料主要要强化基质,减少渣的渗透,减弱变质层的形成。
1 试验
1.1 原料及试验方案
所用骨料为粒度8~5、5~3、3~1和≤1mm的电熔白刚玉,w(AlO)=98.5%;1~0mm的板状刚玉,w(AlO)=98.5%;≤0.074 mm镁铝尖晶石微粉,w(AlO)=78.5%,w(Mg O)=20%;≤0.088mm电熔镁砂粉,w(MgO)=96.5%;≤3μm的α-Al2O微粉,w(AlO)=98.5%;纯铝酸钙水泥,w(AlO)=70%,w(CaO)=29%。按照电熔白刚玉骨料55%(w),板状刚玉骨料10%(w),刚玉细粉、镁砂粉、镁铝尖晶石微粉和α-AlO微粉32%(w),铝酸钙水泥3%(w)进行配料,改变镁砂和尖晶石的含量,详见表1。表1试样配制
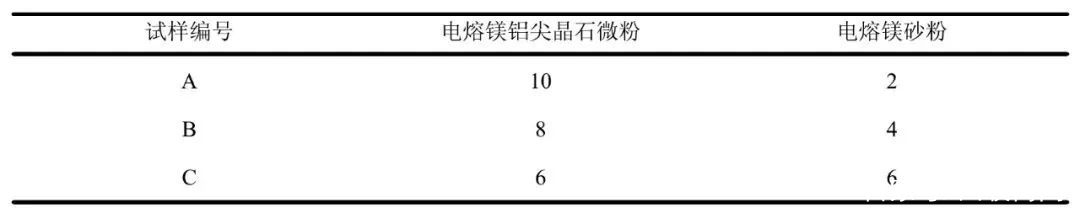
1.2 试验过程和性能检测
将配好的试样振动浇注在40mm×40mm×160mm的模具内,自然养护24h脱模,经110℃保温24h、1000℃保温3h、1600℃保温3h热处理后测定其性能,采用静态坩埚法进行渣蚀试验。沿试样成型方向,在试样顶面的中心钻取深度40mm、内径上下分别为38mm、33mm的孔,制成坩埚,振动成型经110℃保温24h烘烤后在每个坩埚中放入50g渣(渣的化学组成(w)为:FeO24.97%,AlO6.63%,CaO16.13%,SiO9.47%,TiO1.1%,MnO0.2%,NaO0.05%,KO0.01%),放入1600℃电炉内烧结并保温3h,自然冷却后沿坩埚截面切开,测量渣蚀面积和渗透面积,分别计算渣蚀指数(渣蚀面积/原凹槽轴截面积×100%)和渗透指数(渗透面积/原凹槽轴截面积×100%)。
2 结果与分析
2.1 物理性能
不同尖晶石和镁砂加入量浇注料的试样在110、1000、1600℃的气孔率、体积密度、强度见表2,各试样抗渣侵蚀后的宏观图片见图1,各试样侵蚀和渗透指数见图2。表2各温度下不同试样的物理性能。
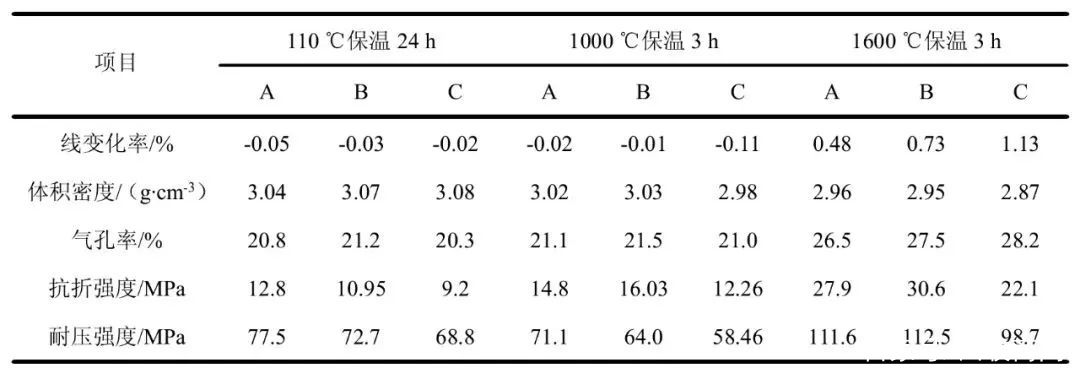
从表2中可以看出,随着镁砂的增加,尖晶石微粉的减少,试样A、B各温度段抗折和耐压强度均高于试样C,中低温度段三种试样强度相差不大,高温段相差较明显。1600℃烧后线变化,三种试样随镁砂含量的增大膨胀量逐渐增加,A试样残余膨胀0.48%最小,气孔率较低,体积稳定性高;而C试样为1.13%,残余膨胀最大。
2.2 渣侵蚀后试样的宏观观察及渣蚀指数
试样的抗渣剖面图见图1。可以看出:三种试样渣侵蚀后外形完整,无明显熔蚀迹象,在1600℃烧后以熔渣渗透为主,渣渗入部位由黑色变为棕色,过渡带由内向外逐渐变浅。剩余渣在凹槽内称圆柱形收缩在中间。试样A产生了横纵裂纹,高温下渣逐渐渗透其裂纹内部,内部残渣量不多,抗侵蚀性一般。试样B渣对坩埚的渗透相比试样A、C的渗透层较浅,残渣量较试样A相比多一些。试样C由于体积膨胀较大,内部气孔较高,渣通过气孔侵入到基质内部,高温下通过液相扩散,使渗透层产生裂纹和结构疏松,坩埚内部残渣量较试样A、B的多。
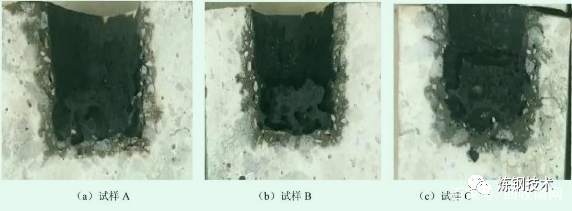
图1 不同试样抗渣试验剖面
试样对渣蚀与渗透的影响见图2。
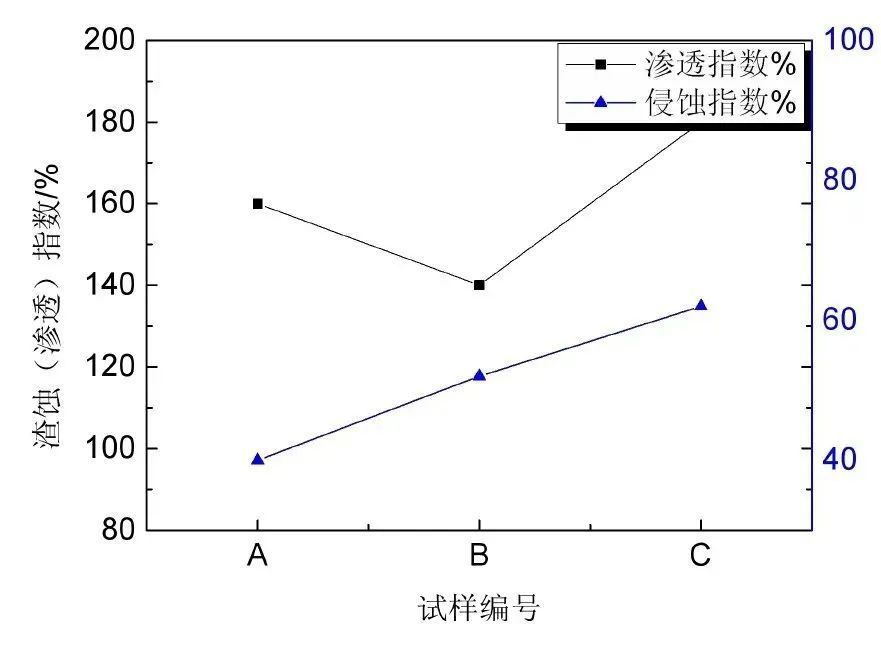
图2 不同试样对渣蚀与渗透的影响
从图2中可以看出,随着镁砂的增加,抗侵蚀指数逐渐增加,抗渗透指数先减少后增加。一方面是镁砂中的MgO与AlO反应原位生成尖晶石产生体积膨胀,过量的镁砂MgO固溶到尖晶石中。1600℃烧后C试样镁砂含量高,合成尖晶石产生的膨胀最大,过量的膨胀却会导致浇注体的高气孔率、低强度,造成渣很容易渗入基质中产生热剥落;另一方面渣中的FeO、MnO可以与尖晶石形成固溶体:FeO+MnO+MA→(Fe,Mn,Mg)O·(Fe,Al)O。使熔渣中的SiO富余而变得非常粘稠。由于渣渗透深度(L)取决于方程式:式中,σ为熔渣表面张力,为浇注体气孔半径,t为渣渗透时间,为浇注体与渣之间的接触角,为熔渣粘度。由此可以推断L与成反比。基质中的AlO能捕捉渣中的CaO,尖晶石加入到浇注料中,能固溶渣中的FeO和MnO,这可提高熔渣粘度和熔点,抑制熔渣渗透,这两种作用可使抗熔渣渗透性的下降抑制在最小的程度之内;另外,随着MgO含量增加,合成镁铝尖晶石中MgO、AlO比值越大,其抗侵蚀能力就越高,所以试样C抗侵蚀指数较试样A、B的高。试样C中的MgO含量较高,膨胀较大,适量的膨胀产生微裂纹可以组织裂纹的扩展,但过量的膨胀产生体积增加,会失去控制熔渣渗透的作用,造成熔渣渗入基质中产生热剥落,导致试样C的渗透指数高。
通过蚀损机制研究得出,由于熔渣与钢包工作衬反应形成了一个保护带,可使内衬不再被熔渣所侵蚀。在这个保护层带中,与内衬接触的熔渣中大部分氧化铁和氧化锰固溶到尖晶石晶格结构内形成固溶体。熔渣中的氧化铁同AlO反应生成铁铝尖晶石所引起的膨胀并不显著。虽然由于渣中的CaO同AlO反应生成CA6会产生很大的膨胀,但却被熔渣中的CaO和SiO同AlO反应生成钙铝黄长石或钙长石等低熔点的矿物反应给均衡了。因此,钢包工作衬同熔渣反应生成高熔点和低熔点矿物的这种结合,为钢包工作衬提供了一个热面保护层,从而使钢包工作衬的进一步侵蚀减至最少。
此外,当熔渣的化学成分渗透入耐火材料中并与之反应式,被渗透的区域主晶体结合下降,而且很容易被冲击流所冲蚀,这就会导致耐火材料进一步暴露,而使未被渗透部分受到化学侵蚀。相反,在没有机械作用消除被渗透部分,由于热温度梯度,化学侵蚀将逐渐变得缓慢并停止。在热循环过程中却会导致渗透层从未被渗透层剥落,因此钢包浇注料结构剥落会受渗透深度的限制。钢包浇注料不同的部位要求也不同,包壁浇注料受到金属包壳的控制,实际应用中不会发生自由膨胀为了较高的使用寿命,要选用高温处理后线膨胀率低的AlO-MgO质浇注料,同时不剥落、耐侵蚀。包底与包壁不同,包底的约束力小,高膨胀材料由于存在膨胀上浮的缺点,难以应用于此处。为了防止拱起和抑制熔渣渗透,体积稳定性高、热震性好的刚玉-尖晶石质浇注料成为包底应用的首选材料。目前B组配方已成功应用于某国内大型钢厂110t钢包包壁部位,平均使用寿命为180~200炉,其中LF精炼30炉,包壁残厚70mm。
3 结论
浇注料的抗渣侵蚀性与抗渗透性往往是相互矛盾的,要根据具体的使用条件权衡抗侵蚀性和抗渗透性。在本试验中,电熔镁砂粉加入量为4%(w),电熔镁铝尖晶石微粉加入量8%(w)时,铝镁质钢包浇注料的抗渣效果较好。